When purchasing building sealant in bulk, you might encounter various suppliers, factories, and trading companies, plus innumerable brands makes and types of sealant that are indistinguishable from each other by product model or technical terminology—in short, it’s very difficult to know which sealant is right for you or what kind of sealants will best meet your needs.
But don’t worry! In this A to Z guide to building sealant terminology, we will bring you all the features & performance hints about building that you need to know for your purchase and help you along your way through the technical stuff you might meet. By understanding these basic terms clearly, you can make more informed decisions and choose the sealant that is most suited to your application.
But first of all, what exactly is a building sealant?
Table of Contents
ToggleWhat is Building Sealant?
Building sealant is a paste-like material composed of base adhesive, fillers, curing agents, and other additives. After it is applied, it cures into an elastic rubber material that sticks to construction substrates, providing sealing, waterproofing, and leak prevention. It is primarily used for sealing and filling joints in buildings.
Building Sealant Types & Sealant Terminology
Building sealant can be categorized using different methods. One method classifies them as Single-component sealants and Two-component sealants. This method is based on how the product is used, whether it is ready-to-use or if you need a mixing machine to use it.
Another popular method focuses on the chemical composition, which directly affects the sealant’s performance in different environments (e.g., UV resistance, elasticity, adhesion to materials). This method groups them into categories such as Modified Silane Polymer Modified Silane Polymer Sealant (MS), Polyurethane Adhesive (PU), and Silicone Sealant (SC). Apart from these two, it is common to classify sealants into sealing, structural, and weather-proof.
Based on the Application Method
Single-component sealant
Single-component sealants normally consist of a single chemical substance and you don’t need to mix it with other substances. They are ready for direct use and are commonly packaged in hard cartridges, soft film sausage packaging, or toothpaste-style tubes. These sealants can be applied by simply squeezing or spraying. For sausage type, we use a sausage gun and a nozzle, and cartridge sealant works with a caulking gun, but you don’t need mixing.
Two-component sealant
Two-component sealants are created by combining two or more chemical substances: component A and component B.
Typically, component A serves as the base adhesive, while component B acts as the curing agent. Fillers and other additives may be included in either component A or B as needed. During use, specialized mechanical equipment (a two-component sealant dispenser) is required to mix components A and B in the specified ratio. A chemical reaction between the two components leads to curing. Neither component A nor component B can be used independently. Some two-component sealants also have a limited working time after mixing; if not applied within this timeframe, the mixture will harden and become unusable.
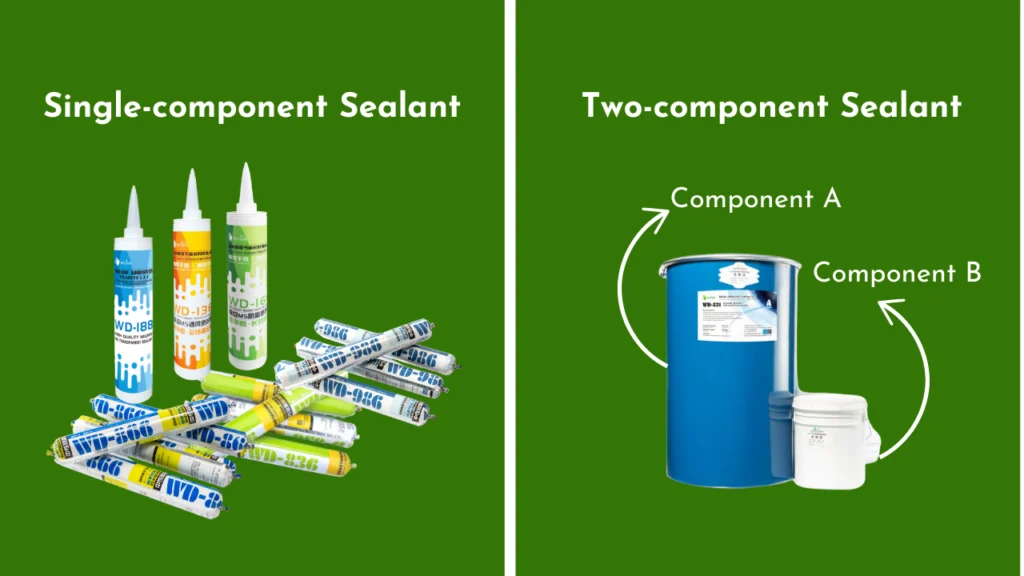
Based on the Chemical Composition
Building sealant can be categorized based on their chemical composition, including Silicone Sealants (SC), Polyurethane Sealants (PU), Modified Silane Polymer Sealants (MS), Polysulfide Sealants, Epoxy Sealants, Acrylic Sealants, and more. In this article, we will focus only on SC, PU, and MS.
Modified Silane Polymer Sealant (MS)
The main component is a modified silane polymer. It has excellent adhesion to engineering plastics such as acrylic, ABS, and plexiglass, as well as porous materials like concrete. It is suitable for various adhesives used in industrial assembly for interior decoration and excels in bonding multiple materials. This sealant is characterized by being non-toxic, odorless, and has low VOC content.
Polyurethane Adhesive (PU)
The main components of polyurethane adhesives are polyisocyanurate and polyols. Theoretically, silicone sealants are more UV-resistant than polyurethane adhesives due to the strength of the silicon-oxygen bond compared to carbon-oxygen and carbon-nitrogen bonds. We can verify this through UV exposure testing; after 240 hours of UV exposure or high-temperature baking, both polyurethane and silicone sealants will show noticeable yellowing. After 720 hours, polyurethane adhesives may begin to show surface chalking.
Overall, silicone sealants are highly resistant to temperature and wear, making them suitable for electronics, construction, and renovation projects, and they are widely used in building sealants. Polyurethane adhesives is resistant to acids and bases, as well as chemical corrosion, making them suitable for road construction, automotive manufacturing, and electronic encapsulation.
Silicone Sealant (SC)
The main component of silicone sealant is polydimethylsiloxane. Silicone sealants actually belong to a large family, including sealants, weatherproof adhesives, and structural adhesives. These products are often used for sealing joints in doors and windows, interior decoration, and insulating glass. In particular, structural silicone sealants can be used in glass curtain walls, stone curtain walls, and steel structures, making their application range very broad. They feature fast curing, no bubbling, and strong adhesion to non-porous materials.
WD Sealant Products:
Based on the function & performance
Sealing Sealant
The main function of a sealing sealant is to prevent water, air, dust and other external substances from entering gaps, ensuring a tight seal. Sealants usually have good flowability and filling properties,, and can easily fill gaps of various shapes and sizes. In the construction field, sealants are commonly used for sealing door and window gaps, pipe interfaces, wall cracks and other places.
Weather-resistant sealant
Weather-resistant sealant is an adhesive that can withstand environmental erosion. They are featured with excellent weather resistance, aging resistance, and UV resistance. In the outdoor environment, weather-resistant sealant can maintain its viscosity and strength for a long period. They are not easy to crack, change color, or lose viscosity. Therefore, weathering adhesive is widely used in building curtain walls, roof waterproofing, bridges or tunnels, and other outdoor occasions that need to be exposed to the natural environment for a long time.
Structural adhesive
Structural adhesive is a high-strength adhesive used to join different materials. Its main features are excellent mechanical properties and the ability to withstand large tensile, applicable to withstand the strong force of the structural parts of the adhesive bonding. Structural adhesive can firmly connect different materials (such as metal, plastic, glass, etc.) together to form a whole. In the building industry, structural adhesive is commonly used in glass curtain wall, steel structure connection, etc.
In the following table, you can review WD sealant products and their corresponding properties categorized under sealing sealants, weather-resistant sealants, and structural sealants.

Technical Indicators & Building Sealant Terminology
We usually find technical terms of building sealant in the Technical Data Sheet (TDS) of the product. They are the data specified in the industry standards, which are used to check the product’s performance and suitability for certain applications. WD Sealant will discuss in future posts how Europe, America, and China have different requirements for these terms. However, in this article, we will explain them in simple words for easy understanding.
Appearance
How the sealant looks depends mostly on how well the filler spreads in the base glue. The filler is a solid powder that, and after it’s mixed by machines, it can disperse evenly in the base, forming a smooth, paste-like substance. Sometimes, depending on the type of filler, there might be tiny bits or fine sand-like particles, which is normal and acceptable. But if the filler isn’t mixed well, you’ll notice bigger particles. Other things, such as mixed-in impurities or skin formation, can also affect the product’s appearance. These issues can also affect how it looks.
These are usually considered rough in appearance. To check the appearance, you can either look at the sealant straight from the package or squeeze squeeze 1-2g onto white paper, fold the paper, press it flat, and then unfold it for examination—this method is called a “butterfly test.”, If you spot coarse particles, you should further assess them.
Curing time
The minimum time required for a building sealant to cure to a rubber-like state (20HS – Shore Hardness). Single-component silicone sealant, its curing process needs to absorb moisture in the air, so the higher the humidity in the atmosphere, the faster the curing speed will be; the lower the humidity, the slower the curing speed. Especially in the autumn and winter dry season, the decline in ambient humidity will extend the ful cured time of the single-component sealant.
Elongation
Elongation is the elasticity of a sealant after it has fully cured, and is also one of the mechanical properties, It refers to the percentage ratio between the total stretch of the material when pulled and its original length. A sealant with good elasticity will have a higher elongation rate.
Extrudability
Extrudability means how easy it is to apply the building sealant. We often talk about whether the sealant is “easy to squeeze out.” Extrudability is directly related to ease of squeezing out rating of the sealant—the higher the value, the easier to squeeze out the sealant, and vice versa. Extrudability can also be affected by factors such as temperature, the type of caulking gun, and packaging. For example, higher temperatures or a larger nozzle opening on the sealant bottle can make the sealant easier to apply.
Hardness
Hardness: Hardness means the firmness of the sealant after it has fully cured into a rubber material. Hardness is one of the physical and mechanical properties of the product. It tells us how well the material can resist being scratched or having something pressed into it.
We have several ways measure the hardness of sealants. If a sealant is too hard, the surface will be firm, but we cannot easily stretch or bend them. On the other hand, if it’s too soft, you will find the sealant too flexible but it lacks strength. So, the right hardness isn’t about being extremely hard or very soft—it needs to be just right for the job you’re using it for.
Sag/Slump
when the sealant is applied on a vertical surface, sag/slump is the sealant’s ability to maintain its shape without sagging or flowing before it cures. It measures whether the sealant will stay in place or slump downward due to gravity.
- Low Sag/Slump: Sealant with low sag/slump is ideal for applications where you need the sealant to hold its shape on vertical surfaces, like walls or ceilings.
- High Sag/Slump: Sealant with high sag/slump is not suited for vertical applications, as the sealant may flow or drop under its own weight.
Tack-free time
The minimum time required for a sealant surface to cure to a tack-free (non-sticky) condition. During the application of sealant, the tack-free time, which shows the surface drying performance, and is directly related to how quickly the sealant dries. The shorter the tack-free time, the faster the drying, the longer the tack-free time, the slower the drying.The tack-free time can be affected by factors such as temperature and humidity, formulation and other factors. Generally, it dries faster in summer than in winter. We can use the “Finger Touch Test” to check the sealant tack-free time, which helps in planning subsequent construction work.
Tensile Modulus and Movement Capability
Tensile Modulus and Movement Capability: Tensile Modulus means stretching strength, it tells us how strong a sealant is when we pull it. Movement capability means flexibility, it shows how much it can bend or move.
- Tensile Modulus (Stretching strength) means how strong the sealant becomes when you stretch it by a certain amount. For example, if we say the sealant has a stretching strength of 0.46 MPa at 25%, it tells us how much strength it has when stretched by 25% of its original length.
- Movement ability (flexibility) shows how well the sealant can adjust when heat or cold makes the materials get bigger or smaller.If a sealant has a movement capability of ±25%, it means the sealant joint can stretch or compress by 25% of its original width. For example, if the original joint is 12mm wide, it can shrink down to 9mm or stretch up to 15mm.
How to test these abilities? We can repeatedly stretch and compress the sealant or we can change the temperatures to see how well it holds up.
Work Life (Tooling Time)
Work life, also known as tooling time, is the amount of time you can shape or adjust the building sealant after it is applied but before it starts curing (hardening). During this time, the sealant stays soft and flexible, so you can still move the sealant around, so you can still move it around, fix any mistakes, or make the joint surface smooth. After this time, it starts to harden and it becomes difficult to make any changes.
- Long Work Life: you will have more time to make adjustments and shape the sealant.
- Short Work Life: The sealant become hard quickly, so you’ll have less time to work with it, but it might be useful in situations where fast curing is needed.